Growing up, I remember my great-grandma telling me about the first time she saw a car driving through rural central Wisconsin in the early 1900s. She described how loud it sounded, the smell of the exhaust, the speed it traveled, and the thrill she experienced on seeing something new.
Life was like that in the early 20th Century in the United States. An excited public looked forward to taking advantage of the progress in technology, science, and manufacturing – all those new things.
US Workplace Safety in the Early 20th Century
The cosmic scales balanced the thrill of advancement with the tragedy of accidental deaths in the labor force that made all those new things.
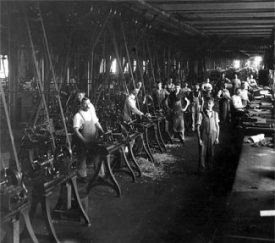
For example, working conditions in US factories weren’t ideal in any real sense:
Factories were not the best places to work. The only light present was the sunlight that came through the windows. Machines spit out smoke and in some factories, workers came out covered in black soot by the end of the day. There were a plethora of machines with few safety precautions. This resulted in many accidents. The workers only received a break for lunch and a break for dinner.
If you worked in the early part of last century, you had four guarantees:
- Low wages
- Long working days/weeks
- No regulations
- No insurance
If injured or killed on the job, the only recourse your family had available to them was to sue the employer. Unfortunately, companies back then weren’t afraid of any lawsuits brought about by the family of injured or killed employees. Most of the time the courts ruled in the company’s favor.
Workplace Conditions Started Improving
After a time, things changed. New York state passed the first worker’s compensation law in 1910, soon followed by other states. The new compensation laws benefited workers, yet those laws appealed to companies, too. Instead of random legal battles and their related costs, compensation laws made costs more predictable and reduced labor conflicts.
As the United States approached the 1910s, safety started becoming more than an interest for companies. The National Safety Council, created in 1913, so companies could pool information. Companies became liable for workplace accidents more often than before. Those rising compensation costs started the search for solutions.
Companies began to guard machines and power sources while machinery makers developed safer designs. Managers began to look for hidden dangers at work and to require that workers wear hard hats and safety glasses. They also set up safety departments run by engineers and safety committees that included both workers and managers.
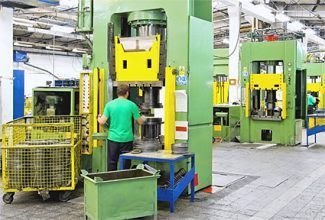
Eventually, workplaces became safer. Between 1913 and today, the US has experienced a 95% drop in job-related fatalities. One of the many reasons for the decline is the use of technology. If a specific task deemed too dangerous to a worker, a form of technology took its place.
During this changing period, several organizations formed with four shared goals:
- Further worker’s rights
- Improve their working conditions
- Coordinate with other nations
- Create a set of standards for industries to follow.
The American National Standards Institute
Initially established in October 1918 as the American Engineering Standards Committee (AESC), ANSI started its first year as an ambitious program and little else. One year after its founding, the AESC approved its first standard on pipe threads. In 1920, the AESC began coordinating the replacement of many rules and laws that hampered the prevention of accidents. Adopted in 1921, the very first American Standard Safety Code protected the eyes and heads belonging to industrial workers.
Early on, the AESC was active in its attempts at promoting cooperation from other nations. In 1926, it hosted the conference that created the International Standards Association (ISA). After World War II, ISA evolved into the International Organization for Standardization (ISO).
The AESC underwent several reorganizations and name changes until 1968 when ANSI formed. Regardless of its name, ANSI increased coordination of voluntary national standards, called the American National Standards. Formalized in 1970 was a public review process. This review process gave the ANSI Board of Standards Review (BSR) the responsibility of approving standards.
The BSR created procedures that determined if standards submitted to the Institute met its guidelines. These new requirements heightened the American National Standards credibility with the public, government agencies, and industry.
In the US, there were several notable recalls in 2007 that put the spotlight on consumer product safety and the global supply chain. ANSI became a leader in the demonstration of the value of standards and conformance, along with consumer safety.
The Business and Institutional Furniture Manufacturers Association
The Business and Institutional Furniture Manufacturers Association (BIFMA), founded in 1973 as a non-profit organization. The organization serves North American furniture manufacturers. As an ANSI-accredited standards developer, BIFMA develops voluntary performance and safety standards using the ANSI consensus process. Once ANSI approves those standards, they’re made public for use by all applicable manufacturers and suppliers. Those companies test products to determine if they meet BIFMA standards and guidelines.
In addition to the voluntary industry and product standards that BIFMA develops, they also:
- Support healthy, safe, and sustainable environments
- Publish key industry statistics
- Advocate for legislation and government regulation with a direct impact on the health of the industry
- Provides a useful forum for members to cooperate and collaborate on appropriate industry issues
The difference between ANSI and BIFMA is simple:
- ANSI covers a wide-range of industries, including office furniture, overseeing and monitoring the process of standards development.
- BIFMA is dedicated to the furniture industry and develops the technical conformance requirements.
Working with the Government
Both ANSI and BIFMA are non-profit organizations. Furniture manufacturers aren’t required to meet standards the organizations develop. Their participation is voluntary. But reputable furniture manufacturing companies know the value of working with both organizations.
Neither organization answers to the US government. Instead, they work closely with its various departments. It’s a relationship of sharing knowledge and collaborating on the creation of new standards. The relationship between ANSI/BIFMA and the US government is a strong one. They share common goals of consumer protection.
The ANSI/BIFMA Tests
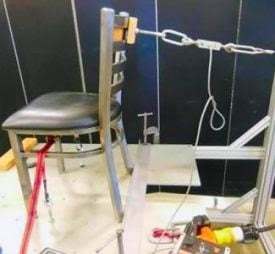
ANSI/BIFMA put in place common standards for desk and table products meant for use in a commercial office environment. Testing facilities that adhere to BIFMA protocols test office furniture durability, structural performance, and safety. The tests include anticipation of product misuse.
Testing facilities that adhere to BIFMA protocols put office furniture through the ringer. There are roughly 50 total tests, but the piece of furniture only needs to meet standards in its category. Some of these tests include:
- Stability Under Vertical Load Test
- Horizontal Stability Test for Desk/Tables with Casters
- Force Stability Test for Tall Desk/Table Products
- Concentrated Functional Load Test
- Concentrated Proof Load Test
- Top Load Ease Cycle Test
- Desk/Table Unit Drop Test
- Leg Strength Test
- Cycle Test for Center/Pencil Drawers
- Interlock Strength Test
- Force Test for Door Locks
- Locking Mechanism Cycle Test
- Work Surface Vertical Adjustment Test
- Keyboard Support and Input Device Support Adjustment Tests
- Durability Test for Desks and Table with Casters
- Pull Force Test
To legitimately claim conformance to any ANSI/BIFMA standard, a piece of furniture needs to meet or exceed all applicable tests. BIFMA continually reviews its testing procedures and releases updates promptly. Updated individual tests should prompt manufacturers to re-test their furniture. BIFMA’s Conformance Guide requires manufacturers to use the current or immediately preceding version of a standard.
Identifying the ANSI/BIFMA Rating for a Product
Passing all the tests in an ANSI/BIFMA standard takes a lot of work. It represents a significant investment for a North American furniture manufacturer. After passing, manufacturers should brag about it and show it off.
A company places any ANSI/BIFMA information on their website or promotional materials. While looking over any furniture you’re thinking about buying, look for a statement that it conforms to relevant BIFMA standard. If you’re not entirely sure, ask the available sales representative.
Why Should I Care?
There are many regulations and laws governing industries. Trade organizations work with their respective industries to coordinate information. Creating both consistent quality and safety standards remains a primary goal for BIFMA.
Knowing that the furniture manufacturer passed all the tests in an ANSI/BIFMA standard reassures any consumer.
In Sum
At the beginning of the evolution of workplace safety and standards, company goals were not altruistic. They were looking to save money. Despite that, companies became concerned about the well-being of their employees. They also started competing in the global economy.
McDonald’s used to brag that a person couldn’t tell the difference between one McDonald’s from another. Because the company standardized their menu and procedures, the food tasted the same. Although that may not be as true today, the overall concept of creating industry standards grew in importance.
My great-grandma told me that after a while, seeing cars and trucks became routine (“…airplanes were cool, though!“). The advent of new industry standards has also become routine to the point where we take them for granted. It’s for this reason that it’s important to know how far things have improved in the last 100 years.
(Updated for clarification. h/t to BIFMA)
COMMENTS